In one of my recent columns, I wrote about the importance of getting your oil temperature up to around 180°F so that your engine would boil off the moisture in your crankcase. This is critical for all engines, but for engines with air-oil separators, that may not be enough.
An air-oil separator is a useful piece of equipment, but must be installed correctly.
As an aircraft engine increases in hours, it may see increased ring wear, which can reduce the sealing performance of the engine. This means that more combustion gases get past the rings and blow into the crankcase.
This “blow-by” will usually vaporize some engine oil that is in the ring belt area. When the blow-by reaches the crankcase, it is sucked out the breather tube into the atmosphere where the oil is instantly condensed and usually sticks to the belly of your aircraft.
Some people say that the oil will make your aircraft slippery so it goes through the air better, but most people do not like the looks of it and the fact that the plane “marks its territory” once it is parked.
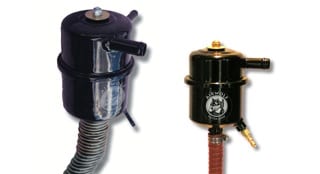
An air-oil separator from Air Wolf
To reduce this problem, some people have installed air-oil separators. The principle for these separators is that they are designed to cool the blow-by gas leaving the engine so that the oil will condense back to a liquid state.
The equipment is set up in such a way so that the condensed oil is returned to the crankcase and then only the combustion gases are blown out the breather. Does anyone see a problem here?
Many years ago, we found some engines with air-oil separators that were having rusting problems even though the oil temperatures were in that 180°F range.
On one of these aircraft, they installed a container between the separator unit and the crankcase. I was shocked when we looked at what was in the container. It was a mixture of water and oil that looked like dirty mayonnaise.
The problem was that the separator unit was not located in the proper location, so it was running at a temperature that condensed both the oil and the water vapor in the blow-by gases and returned it to the crankcase.
The pilot had gone to all of the work to get the crankcase oil temperature up to boil off the moisture, but the separator just returned it to the crankcase.
So are air-oil separators bad? No, but it is very critical that they are installed correctly so that the separator unit is well above 212°F during flight, even in cool weather.
Many people will install the unit in a more convenient location where cool air may reduce the temperature enough so that the unit can condense the water vapor.
If you have an air-oil separator on your aircraft, you should install a temporary temperature gauge on the separator unit itself so that you can monitor the temperature in normal cruise conditions. If your separator unit is around 212°F or less, you may need to relocate it to a spot where it gets less cooling air flow and/or more engine heat.
The devil is in the details.
Source: http://generalaviationnews.comThe No. 1 rule about an air-oil separator