At most of my seminars, there is always a discussion about water in fuel, where it comes from and what steps need to be taken to guard against any problems because of it.
So, where does the water come from? Most of it comes from condensation.
All hydrocarbon fuels, like 100LL and Jet A, will absorb a small amount of water until the fuel reaches its saturation point.
Now this is not a huge amount of water. It is like a few parts per million (ppm) but, with large volumes and over time, it can represent a significant amount.
The problem is that the amount of water that the fuel will hold is directly related to the temperature of the fuel.
When fuel leaves the refinery, it enters a tank warm and it will absorb water out of the air until it reaches its saturation point. Then as the fuel cools, the ppm of water that the fuel will hold decreases so the water that the fuel will hold also decreases.
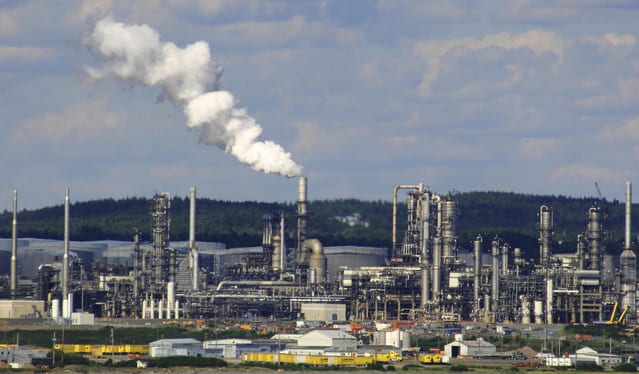
An oil refinery. (Photo courtesy FreeImages.com/William Picard)
The extra water in the cooled fuel will then drop out as free water and fall to the bottom of the tank. There can also be free water from poor housekeeping, like leaking floating roofs on storage tanks.
The bottom line is there is always going to be water in the fuel distribution system.
With that in mind, the distribution system for aviation fuels is designed to safely deal with the water.
The first step is in the large distribution and refinery tanks. They are designed with water draught points so that the free water can be removed periodically.
Unfortunately, these large tanks tend to shift and settle over time so that the water drain ends up being at a point that does not drain all of the free water.
In all of my years of looking at old tanks, I have yet to see a tank in which the water draught will drain all of the free water from the tank.
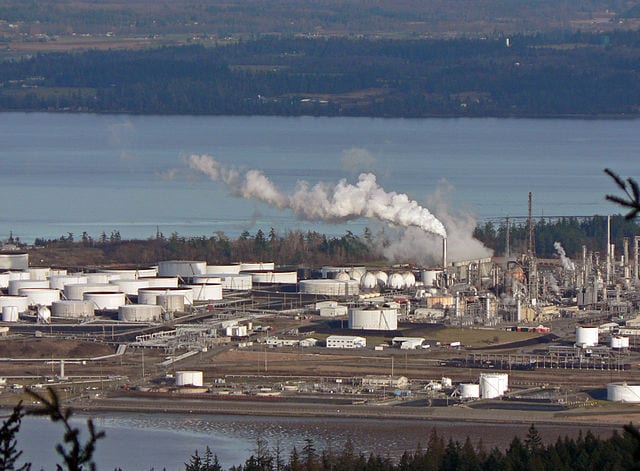
Tanks at the Shell factory in Anacortes, Wash. (Photo by Walter Siegmund)
The other safety feature is that most aviation fuel tanks have floating suction lines. This means that when fuel is pulled from the tank, it does not pull off the bottom of the tank where the free water is. It pulls fuel off near the surface so there should be no free water in the product.
Here again, there can be a problem with old tanks because floats can sink and the swing arm can bind up, resulting in the suction arm pulling fuel off the bottom and picking up some free water.
Another problem is that when fuel is added to the tank, it stirs up the free water off the bottom and it takes a while for it to settle back out.
In most plants there is a specification that requires that no fuel can be pumped out of a tank until a specified settling time after fuel was added to the tank. These times are usually listed as minutes per foot of tank height. But with a tighter economy, some people tend to rush this.
The next step of protection is the filter/separator. These have a unit that coalesces the fine water particles into larger droplets. The second part of the unit is a fine Teflon-coated screen through which the fuel flows freely, but the water droplets do not and settle to the bottom where they can be drained off.
A concern here is surfactants and bugs. These can disarm the separator elements and allow water to pass through the unit. Surfactants are things like detergents and additives that are used in automotive gasoline. These problems have increased now that almost all 100LL is shipped by tank trucks, many of which are also used to haul auto fuels.
What all of this means is that there is a real possibility that you can get some free water with the fuel that you put into your aircraft tank. In addition, you can get free water from condensation from the heating and cooling of the fuel in your aircraft tanks, plus things like poor fitting gas caps on your tanks and poor housekeeping along the way.
So what is the big problem with water? With piston-powered aircraft, the water is heavier than the fuel and it will tend to collect in the carburetor float bowl until it reaches the main jets, at which time the engine will cease to run.
There are also corrosion concerns with water in storage and aircraft fuel tanks. The water will be a collection point for bugs and surfactants, which can be very corrosive for fuel tanks. This is especially critical on Jet powered aircraft.
Water can also freeze, especially at altitude, which can stop adequate fuel flow to the engine.
So what should a pilot do to ensure safe operation? First, always sump your tanks before flight. This can be a pain, especially on low wing aircraft, but I cannot stress the importance of this step enough.
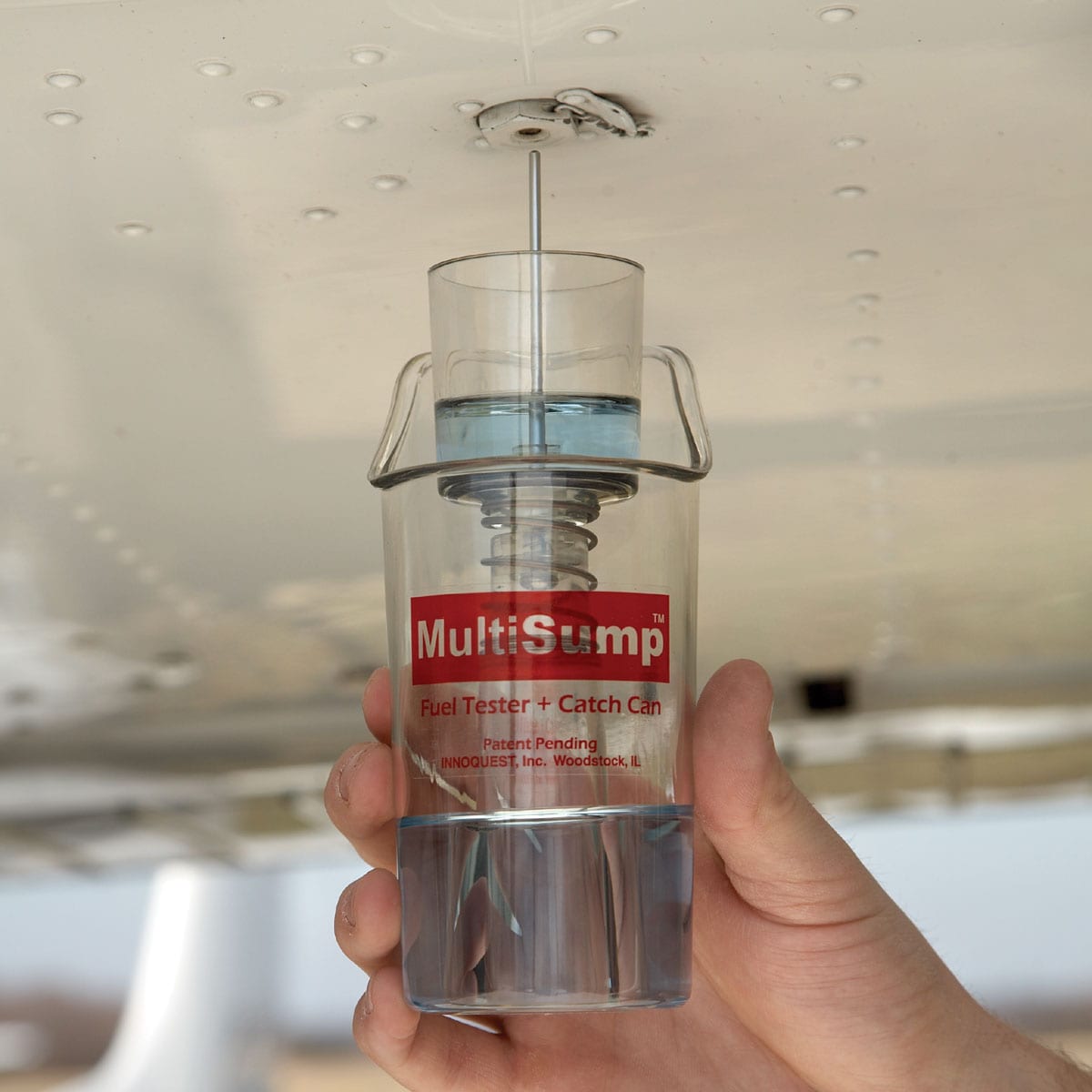
Fuel sump. (Photo courtesy Sporty’s)
Second, know your FBO and make sure it follows all of the necessary checks of their fuel system.
Third, know your plane. Check your fuel caps and make sure the gasket is sealing properly. It is also important to check your tanks. Some of the bladder equipped tanks can have ripple bottoms that can hold water that does not flow freely out the water draw when you sump your tanks.
It is not a question of if there is water in the aviation fuel system. The water is going to be there, so it is critical that all of the safety steps are followed to minimize the risk that it represents.
Source: http://generalaviationnews.comWater: Can’t live without it, can’t fly with it